Engine Room Blog 12/01/2006
by Chris Carey & Engine Room Staff
Now that the science has finished for this
cruise, the Engineers have been asked to contribute a piece
to keep the web-readers interested before we get to Cape
Town.
|
Left to Right, the Engine Room department consists of the following
people:
ETO (Electro-Technical Officer) –
Jim (‘ll fix it) McIntyre
Motorman – Les Hillier
Chief Engineer – ‘Sam’
Moss
Second Engineer – Steve Bell
Third Engineer – Keith Connor
Third Engineer – Chris Carey
(front) |
A few facts and figures to start with:
We have four marine diesel engines coupled
to electrical generators that supply all of Discovery’s
power needs. The total power output is approximately 3,000kW,
which is enough to light 50,000 light bulbs. It is also
roughly the same output as 35 basic Ford Focuses! We can
carry a maximum of 512 tonnes of Fuel Oil and we burn on
average 7.5 tonnes per day. We carry 208 tonnes of fresh
water for drinking, cooking and washing purposes. The Fresh
Water tanks are filled to capacity before we embark on a
cruise and to avoid running out of water we make our own
through two evaporators in the engine room. Together they
produce around 8 tonnes of water per day and depending on
how many showers the scientists and crew take, the usual
consumption is 12 tonnes per day. The single propeller is
turned by a giant electric motor that is one of the few
remaining items of original 1962 machinery to be kept on
after the ship was rebuilt in 1992 to bring it up to modern
standards. The original Main Engines were replaced at this
time.
We prefer to keep our lives in the engine
room as trouble free as possible. In order to do this we
use a computerised Planned Maintenance (PM) system. Every
month we get a printout from the computer with a list of
scheduled tasks to complete. The basic principle behind
planned maintenance is that a little work every now and
again helps to keep the machinery running properly for longer
and any faults that do manifest themselves can be nipped
in the bud before serious damage is caused. Much the same
as looking after your car the jobs consist of things like
cleaning filters, checking oil levels, taking measurements
and recording running parameters, ensuring bolts are tight
and routine overhauls and replacement of consumable parts.
For the most part this system runs very efficiently and
we are lucky that we do not suffer many breakdowns of the
plant. Major overhauls of the Main Engines are carried out
when the ship goes into a dry dock, or refit period. After
the de-mobilisation in Cape Town the ship is entering a
25 day refit programme that will see the complete overhaul
of two of the Main Engines. Cylinder heads, pistons, cylinder
liners and crankcase are cleaned, inspected and measurements
taken to ascertain their continuing life expectancy –
parts being replaced if they fall out of tolerance with
manufacturers limits. A third engine is due to have its
cylinder heads removed for cleaning and overhaul. There
is also some repair work being carried out to the Propulsion
Motor. Some of the copper windings are being removed for
repair and re-insulating, damage caused by years of continued
use and prolonged heat.
Main Engine & Generator |
View of Propulsion Motor &
Thrust Bearing |
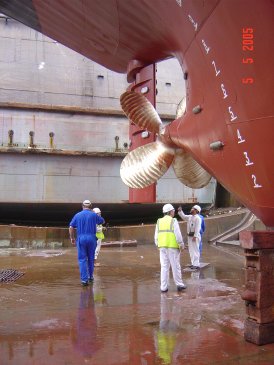 |
The Engine Room operates on a UMS system, (Unmanned Machinery
Space). This means that the Engine Room does not have
to be continuously manned by watchkeeping Engineers.
Instead we work from 8am to 6pm, and every night there
is a Duty Engineer who is on call to answer any alarms
that may occur during his duty period. We each take
it in turns to carry out a duty day and the Duty Engineer
is responsible for keeping the daily service fuel
tanks topped up, pumping out waste water from the
engine room bilges, logging the running parameters
of the propulsion plant and basically keeping an eye
on things to make sure the engine room is run cleanly,
efficiently and safely at all times. An Engineer can
use all five of his senses when carrying out his rounds… |
Touch:
|
Is something hotter,
colder than usual or vibrating? |
Sight: |
Are there any oil / water leaks? |
Hearing: |
Is an engine or pump making a noise
that it usually doesn’t? |
Smell: |
Smelling fuel oil may mean there is
a leakage. |
Taste: |
Can’t see where that water
is dripping from? Taste to see if it’s fresh
or salty – it’s a good start to identifying
the source! (It’s also a good idea to sniff
it first to make sure there are no chemicals!) |
The Motorman is an invaluable resource in
the Engine Room. Every day he starts by cleaning down the
Main Engines and then tops up the sumps with fresh oil if
they require it, then whips a mop around the floor plates
to remove any dirt, oil or grease that could be a slip hazard.
Woe betide any Engineer who leaves a mess after they finish
working! After that he sometimes assists the Engineers if
they require extra help with a task, or out comes his paintbrush
and roller to smarten up the Engine Room. Since the dry-dock
last May the motormen have repainted the motor room, engine
room floor plates, ETO workshop, Engineer’s workshop
and incinerator space. The transformation has been amazing
and the fresh coat of white paint on the bulkheads (walls)
has let us all see the engine room in a new light!
In the afternoons it is his responsibility
to burn any garbage accumulated by the ship. Usually a collection
of oily rags, paper and cardboard is burnt. Plastic can
also be burnt, but has to be done independently as the ash
has to be specially disposed of. The incinerator is also
used to burn waste oil sludge from the Engine Room.
The ETO is also on day-work (although he is
on call 24 hours a day) and he is responsible for maintaining
and repairing the electrical side of the ship’s systems.
His talents run from changing fluorescent tubes to fathoming
the intricacies of the Scientific Winch control system.
With the introduction of complicated PLC logic controllers
into so many of the ship’s systems in recent times,
the ETO is a very valuable person to have around when things
get a little tricky!
The Engine Room is always a noisy place to
work. We are all very careful to ensure that our ears are
properly protected – either with ear defenders for
prolonged exposure, or disposable ear plugs for short periods
of time. Whatever ear protection is used, the materials
filter out the damaging high frequency sound waves and muffle
the other sounds. We can still detect abnormalities in the
sound of the running machinery quite easily although conversation
is tricky unless you shout close to another person’s
ear!
Another factor of engine room work is heat
– or sometimes the lack of it! This cruise has seen
us leave a hot Port Elizabeth where the engine room temperature
was around 40ºC. At Crozet it was less than 15ºC
– especially under the ventilation blowers! Now on
our way back up to Cape Town it is rising again to around
the 40ºC mark. When it is that hot, we take regular
breaks from the heat by cooling off in the workshop, office
or Control Room. Plenty of water is drunk to replace the
fluid lost from sweat and we also take re-hydration solutions
to replace the salts. On the flip side, down in Crozet we
had to resort to wearing t-shirts under boilersuits, or
even wearing a jacket on the really cold days!
It’s certainly an interesting job in
the Engine Room, and every day is different. We happen to
be lucky on this cruise as we make a very good team and
we feed off each other for experience and ideas.
I hope you’ve enjoyed reading about
or lives “down below” and it has given you an
insight into the areas that are not often seen by the scientists
on board.