Our research projects
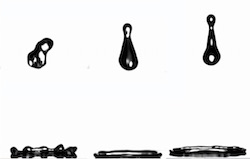
Some of our current and recent projects are described below
Industrial collaborations
We work together with a number of Companies to solve specific technical problems, develop practical applications of our research, or simply try crazy new ideas (sometimes they work!).
Recent industrial partners include Brooks Automation and Life Sciences (Irlam, UK) and NeedleSmart Ltd. (Knowsley, UK).
Materials & Manufacturing
Low-temperature synthesis and inkjet printing of photoactive TiO2 films
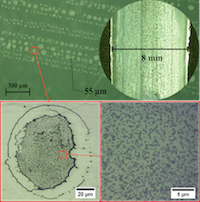
We developed a low-temperature method to synthesize and inkjet-print photoactive TiO2 films on polymeric substrates using a commercial inkjet printer. Low-temperature synthesis and inkjet printing methods would cut down the process costs and provide the possibility for using a wide range of materials such as polymers in catalysis and coating technologies. The printed substrates were used in a polymeric microfluidic reactor fabricated by selective transmission laser welding. The catalytic activity of the printed nanolayers was studied based on the photodegradation of methylene blue as a standard pollutant. The performance of our synthesized TiO2 is superior to commercial TiO2 nanopowders. Furthermore, the coated catalyst remains active and intact even after a long-term reaction run. The entire process of synthesis and printing is carried out through a calcination free route below 100°C.
H. Maleki, V. Bertola, TiO2 nanofilms on polymeric substrates for the photocatalytic degradation of methylene blue, ACS Applied Nano Materials, 2019.
Multiphase Flow & Complex Fluids
Oil-water flow in a serpentine channel
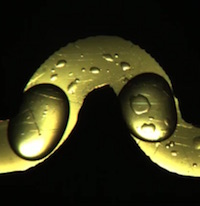
We studied the co-current oil-water flow in a horizontal serpentine channel by high-speed imaging. Due to the channel geometry, the flow exhibits curved streamlines, which can induce secondary flows and alter the flow pattern transition boundaries in comparison with those observed in straight channels. This can have important applications in the development of microfluidic mixing devices. The serpentine channel was cut out in a black polypropylene sheet sandwiched between two transparent polypropylene sheets and bonded by selective laser welding. Different flow patterns were generated by changing independently the superficial velocities of the two fluids using a dual-drive syringe pump. Results enabled the construction of a flow pattern map, which shows significant differences with the equivalent map obtained for straight microchannels.
Impact of viscoplastic drops on viscoplastic surfaces
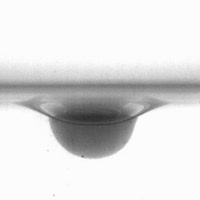
The interaction between viscoplastic drops and surfaces has an important application in additive manufacturing, where a fresh layer of material is deposited on a partially cured or dried layer of the same material. So far, no systematic studies on this subject have been reported in literature. We studied by high speed imaging the impact morphology of different drop/substrate combinations, with yield stresses ranging from 1.13 Pa to 11.7 Pa, for impact Weber numbers between 15 and 85. Experimental data were compared with one of the existing models for Newtonian drop impact onto liquid surfaces. Our results show the magnitude of the yield stress of drop/substrate strongly affects the final shape of the impacting drop, which remains permanently deformed at the end of impact.
S. Chen, V. Bertola, Morphology of viscoplastic drop impact on viscoplastic surfaces, Soft Matter, vol. 13, pp. 711-719, 2017.
Impact of dilute polymer solution drops on solid surfaces
Old projects
Heat Transfer
Flexible pulsating heat pipes built with plastic materials
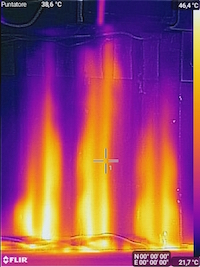
We have developed a novel type of flexible, lightweight and low cost pulsating heat pipe built with a thermoplastic material (polypropylene), which can be advantageous for space, aircraft and portable electronic applications where the device weight is crucial. Although the thermal performance of thermoplastics is usually poor, our technology enables the creation of composite thermoplastic materials having a significantly enhanced thermal conductivity. The basic concept is to sandwich a serpentine channel, which is cut out in a polypropylene sheet and contains a self-propelled gas-vapour mixture, between two transparent polypropylene sheets, bonded together by selective laser welding. This results into a heat transfer device with a large surface and very small thickness (approximately 1.5 mm), which makes it suitable for many existing and future applications where thermal management is not possible using existing technologies.
O. Der, M. Marengo, V. Bertola, Thermal Performance of Pulsating Heat Stripes (PHS) Built with Plastic Materials, Journal of Heat Transfer (Transactions ASME), vol. 141(9), 091808, 2019.